









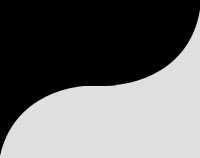
|
 |
eng||rus
Microplasma Technology for improving the quality of metal-ceramic dentures
- The Institute of General Physics of the Russian Academy of Sciences, in collaboration with Plasmaiofan Co., Ltd. Science and Technology Center, developed the physical principles of a new energy-saving microplasma technology for the adhesion of ceramics to metals and alloys.
- The proposed microplasma technology is based on the principle of hardening metal articles by converting the energy of contracted microplasma discharges excited on the metal surface into heat. This leads to the formation of a flowed surface layer and a reduction of the number of structural defects per unit area of the surface. As a result, the microrelief pattern of the metal surface becomes substantially more pronounced, so that the area of adhesion of ceramics to the surfaces of metals and alloys increases considerably.
- The energy of a quasi-homogeneous (over the metal surface) pulsed-discharge plasma is concentrated by exciting contracted microplasma discharges, which are localized predominantly at defect sites and microcracks. A rapid cooling of the material at local surface sites by means of heat transfer from the surface inward leads to a restructuring of metal surfaces. This effect, together with the smoothing of microcracks and melting of the defect sites, acts to facilitate the hardening of the surface layers, without causing significant heating of the articles or any changes in their internal structure. Simultaneously, the microrelief pattern of the metal surface becomes substantially more pronounced (the area of adhesion increases by a factor of 3 to 5).
- The use of plasma in order to achieve the hardening of metal surfaces resolves the problem of a uniform processing of metal articles with a complicated surface structure.
- The effective rate at which the surfaces of metal articles are processed amounts to tens of square centimeters per second (recalculated for the duration of pulsed discharges), the electric-power consumption being unprecedented, specifically, much less than 0.1 of a kilowatt-hour per square centimeter of the processed surface of an article (in particular, of a denture).
- The optimum hardening regimes achievable in the microplasma technology offer the following advantages:
for articles made of 45 steel, the microhardness of a surface layer with a thickness of up to 20 mkm can be increased by a factor of up to 10, the friction coefficient can be lowered by a factor of up to 10, the maximum possible pressure can be raised by a factor of up to 18, and the wear rate can be reduced by a factor of up to 4;
for articles made of VT-1 titanium alloy, the microhardness of a surface layer with a thickness of 2--7 mkm can be increased by a factor of 2 to 14, the friction coefficient can be lowered by a factor of up to 3, the maximum possible pressure can be raised by a factor of up to 3, and the wear rate can be reduced by a factor of up to 4;
for articles made of V-95 aluminum alloy, the microhardness of a surface layer with a thickness of up to 16 mkm can be increased by a factor of up to 2, the friction coefficient can be lowered by a factor of up to 3, the maximum possible pressure can be raised by a factor of up to 5, and the wear rate can be reduced by a factor of up to 2.
- The microplasma technology is environmentally clean, generating no pollutants. Our institutions have priority in the development of the microplasma technology. Outside the Russian Federation, research in this field is still in its infancy.
- At present, according to the resolution of the State Committee on Priority Directions in Research and Technology, the Institute of General Physics, together with some other Russian institutions, is developing and constructing experimental devices designed to implement the microplasma technology in medical engineering, in particular, in such branches of stomatology as orthodontics and dental mechanics.
- This is a proposal for cooperation in research on optimization and testing of the microplasma technology with the aim of implementing it in medicine and stomatology as well as in other related branches.
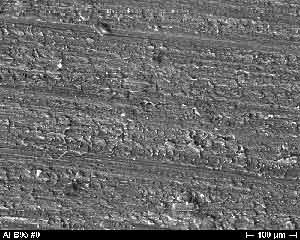 | 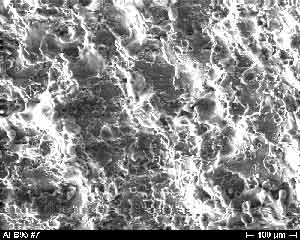 |
Microphotographs of a part of the surface of a sample made of V-95 aluminum alloy after mechanical treatment (left) and after processing by the microplasma technology (right). |
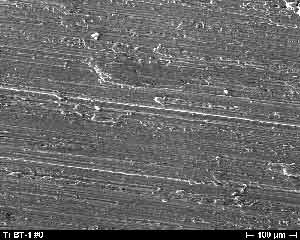 | 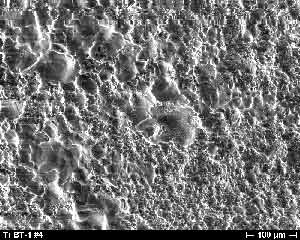 |
Microphotographs of a part of the surface of a sample made of VT-1 titanium alloy after mechanical treatment (left) and after processing by the microplasma technology (right). |
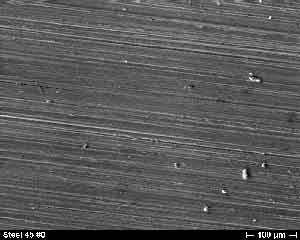 | 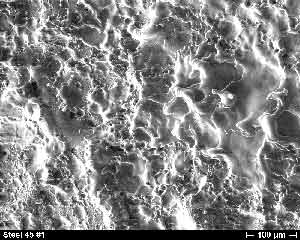 |
Microphotographs of a part of the surface of a sample made of 45 steel after mechanical treatment (left) and after processing by the microplasma technology (right). |
Back
|
|
 |